2x4 Foot N Scale Layout: Building the Benchwork
- Stephen Strum
- Feb 17, 2023
- 11 min read
Updated: Apr 2, 2024

In this post I’ll go over the construction of the benchwork for the 2x4 N Scale project layout I’m working on in early 2023. First off, here is a material list for what I used to build all the layout benchwork. You can watch the YouTube video version at the end of the blog post.
By the way, if you appreciate the weekly YouTube videos and blog posts I’ve even doing for the past 2-3 months, consider buying me a cup of coffee so I can keep running on five hours of sleep a night to keep working my day job and spending a couple hours each evening and early morning working on these train projects, videos, and blog posts: https://www.buymeacoffee.com/stephenstrum
The money actually goes towards better video and audio equipment plus additional lighting panels.

This isn’t necessarily the best use of supplies and the cheapest way of doing things. I used individual 2x4 foot birch panels along with four foot long pieces of poplar as well as a six foot piece of pine. Cutting the birch panels from a 4x8 foot sheet and using longer pieces of lumber would probably be cheaper, but with the small size of all the pieces I was able to fit all the materials in the backseat of our smaller vehicle and it was easier to make sure the plywood pieces I selected weren’t warped and were all the same size.

With most projects I like to try at least one new idea out and on this one I wanted the base to be sturdy, but also light weight. Since it is only 2x4 feet in size it wasn’t going to be too heavy anyway, but being three levels, I wanted to save some weight here and there. So, for the base of the layout, I decide to try using 1/4” thick birch plywood with a layer of 1” insulation foam in the middle. With everything glued together, I figured it would be extremely rigid, but still very light weight.
I used birch plywood, since that weighs less than regular plywood made out of pine, plus usually has a smoother surface. The foam layer makes everything more rigid and allows for a place to run wires. I should have cut channels for wires ahead of time, but it was easy to drill them later with some of my long drill bits. If I was doing this again I might just use a 24” hollow core door and cut it to length, and then fill in the cut end with some plywood pieces or a piece of dimensional pine lumber.

Since I needed to be able to attach wood sides to the layout base in some way, and the 1/4” plywood and the foam layers weren’t going to hold screws or nails well, I added blocks around the perimeter cut from 1/2” plywood that I had on hand.
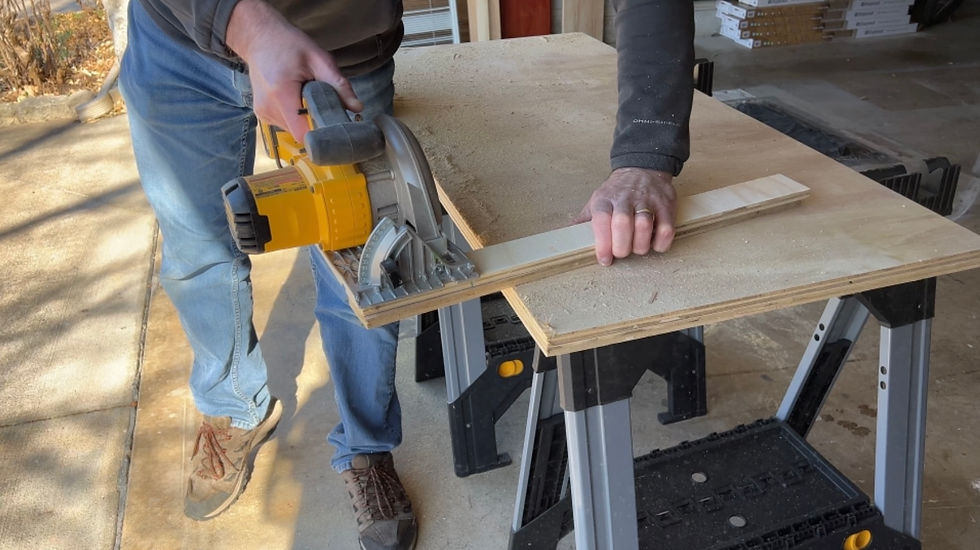
I needed a wood layer that was 1” thick to equal the thickness of the foam board, but dimensional lumber, like a 1x2, is only 3/4” thick. I could have cut down some other wood into a 1” thickness, but the plywood worked well and was readily available.

Again, just buying a door would probably work out easier, or doing regular framing on a half inch thick piece of plywood would be an easier option. Anyway, I stacked up the plywood blocks in the corners and the in the middle of each side along with the very middle of the layout. I cut out sections of foam where the blocks were going to go, and then glued down the foam with foam safe construction adhesive and the wood blocks with wood glue.

Then I applied more glue and adhesive on top of the foam and wood blocks before attaching the top layer of plywood. What I should have done was to take a putty knife and spread out the foam board adhesive or simply used wood glue on everything as it was hard to squeeze everything together to get a avoid a gap between layers. So, I walked over the top of the layout base to help squish everything together.

I tried clamping things together, but I didn’t have enough clamps for that to work, plus couldn’t squeeze the middle areas together well. So, instead I stacked weights on the base. I eventually grabbed my punching and kicking bag my son and I use for TaeKwonDo practice, since that weighs about 250 pounds, and put that on top of the base to squish everything flat while things dried. I also put a few screws into the wood blocks which helped clamp the corners down.

Once things were dry, I removed the screws since they weren’t really needed, and you can see that I ended up with flat, rigid, and very light weight panel.

I sanded the sides with a sanding block, but grabbed the orbital sander for doing the edges. In some places the wood blocks were poking out beyond the edges of the plywood panels a bit, and so those all needed to be sanded down.
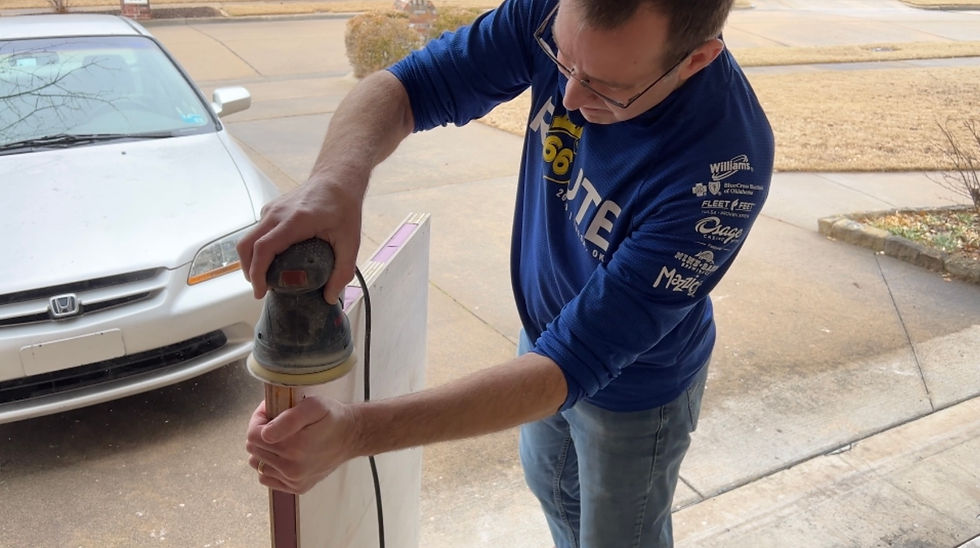
Next, I worked on attaching the sides to the layout base. I used half-inch thick poplar boards that were 6” wide and 48” long for the layout sides, but 1x6 inch clear pine boards would work well too. I clamped a 1x3 along one edge to act as a temporary spacer, and then applied a layer of wood glue to the edge of one side of the layout base. I apparently didn’t want you to see what I was doing, so I worked on things somewhat off camera. Using my brad nailer, I put a few brads into each end and in the middle of the back panel. You could also just use wood screws in those same locations, but using screws isn’t quite as fun as using a nail gun.
This is my nail gun by the way: DeWalt Cordless Brad Nailer: https://amzn.to/3XBvltD
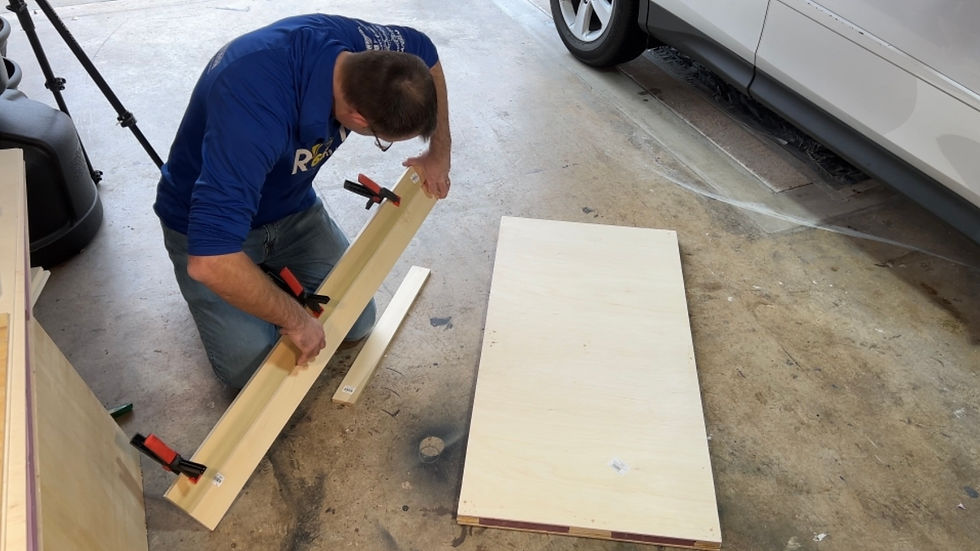
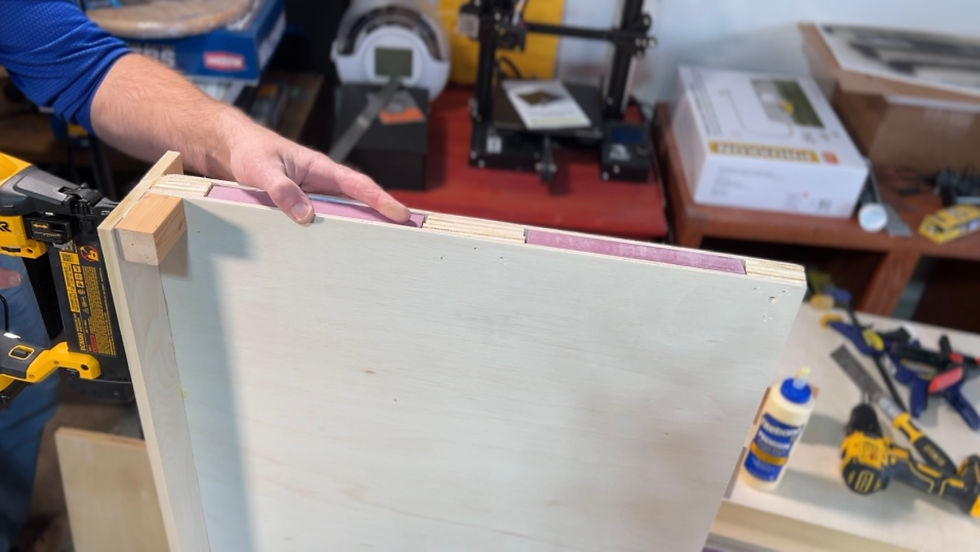
With the back attached to the first level of the layout, I cut another poplar board to size for one of the layout sides, and then cut some pieces off a 2x2” pine board to help brace the corners. I glued and nailed a 2x2 pine block to one of the corners, but had to use a clamp to help squeeze the block back against the back board. I did the same to the other back corner of the layout.

Then, I clamped another 1x3 to the edge of the side board to act as a spacer guide again, applied glue to the layout side, then put some brad nails into the wood blocks in the layout base to secure everything. I flipped the layout over and attached the other side in the same way.
At this point I went ahead and grabbed the plates for attaching legs to the base of the layout along with some of the legs I had on had. I have some short legs that are about 4” long, some longer legs about 28 or 30” long, and then some that are only about 20” long but have casters attached. The legs with casters came from an old 4x8 HO scale layout I used to have that was built from the Woodland Scenics Grand Valley Layout Kit.
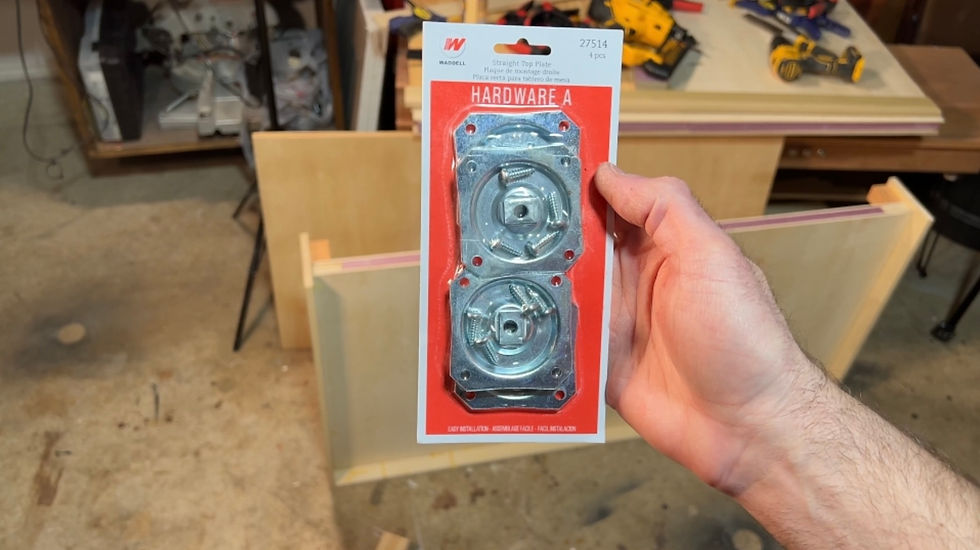
I screwed the mounting plates to the bottom of the layout, to temporarily add the longer legs. I did eventually come back and add some mounting blocks on each corner of the layout so the plates would have more structure to hang on to.
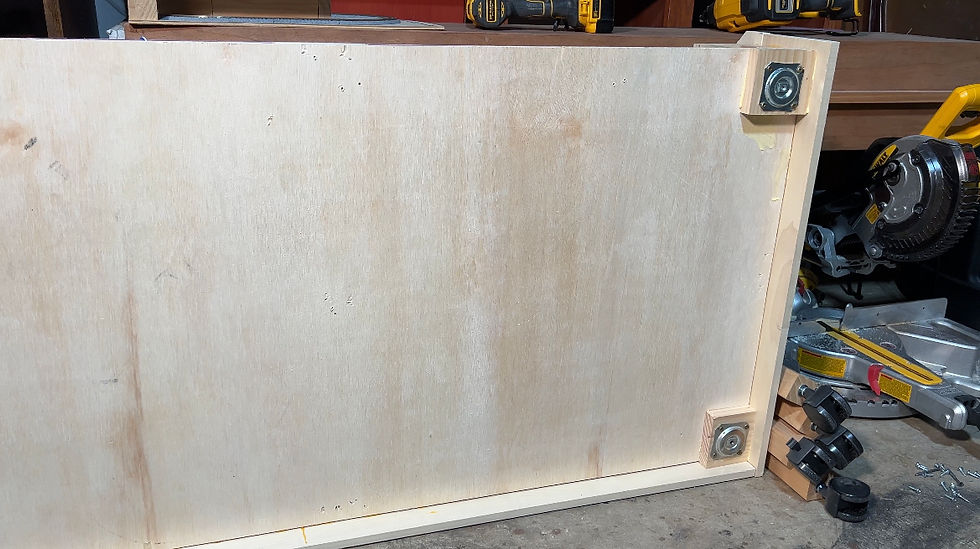
Once the plates were attached, I threaded on the legs, and then had a layout that I could easily roll around the garage as I worked on it.

Before working on the next level of the layout I needed to get the track temporarily put in place on the lowest level. That way, I could make sure none of the wood supports for the second level would cause clearance issues with trains on the first level.
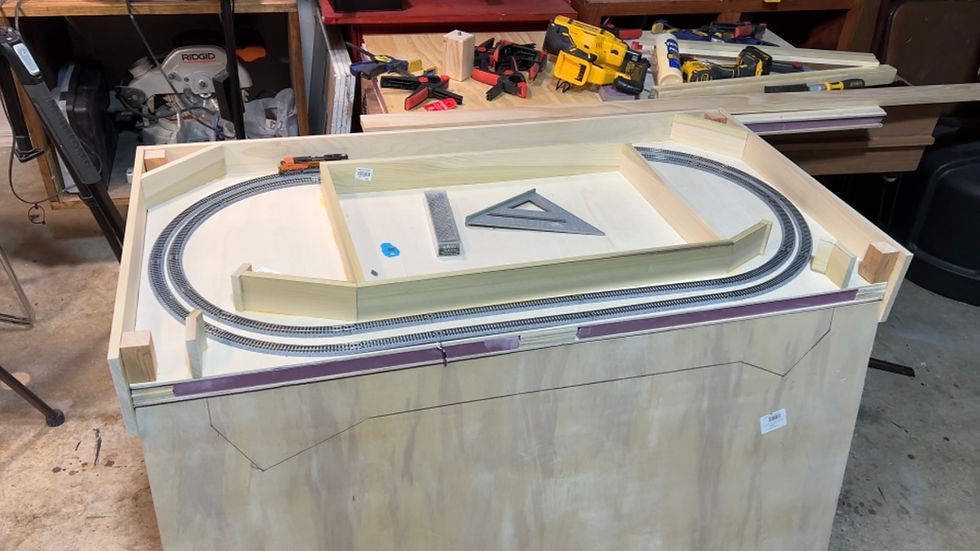
The outer loop of the lower level uses 11” radius curves and the inner loop uses 9 3/4” radius curves. I added a set of terminal rail joiners so I could power the outer loop and run a longer locomotive to make sure there would be no clearance issues as I worked on placing in the support structure.
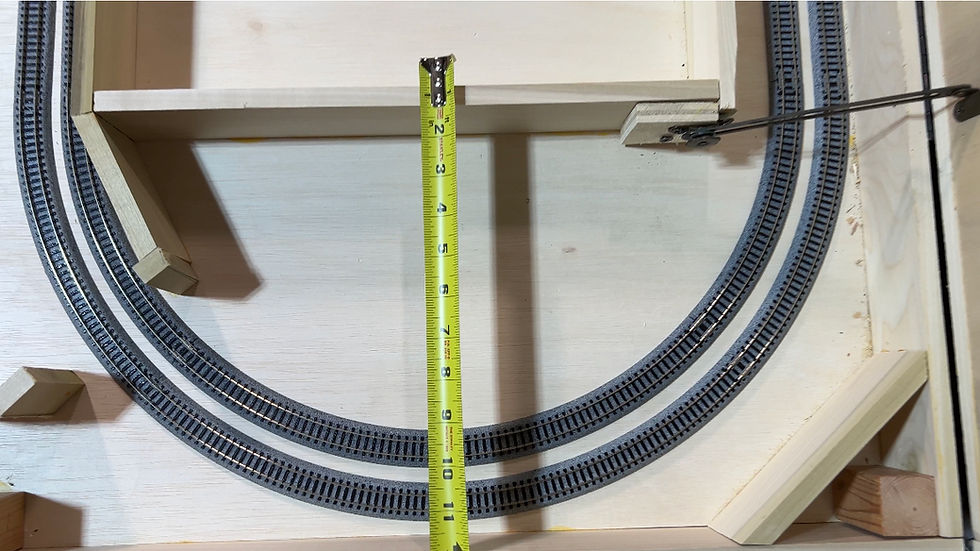
This is the list of Kato track needed for each level and loop. In the next video in this series I’ll be installing the track and doing the basic wiring for the layout, so I’ll be going over the track installation in more detail in that video.
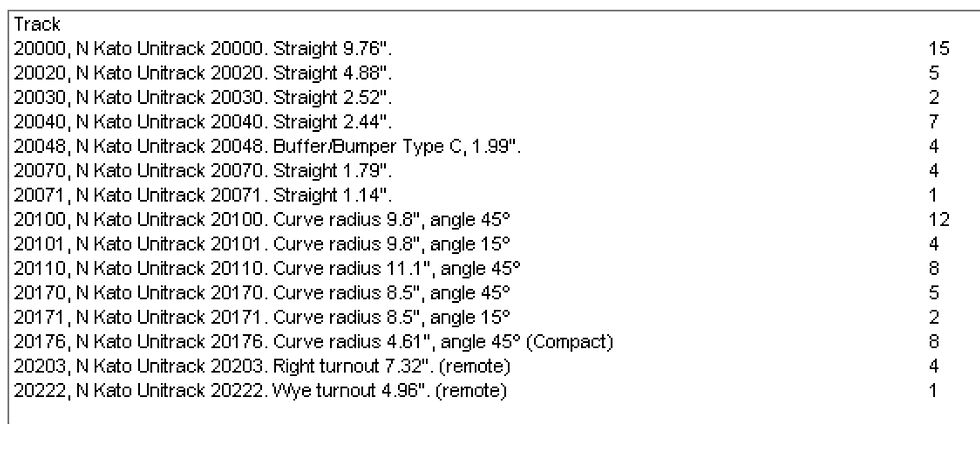
The half inch by three inch poplar wood supports in the front would both act as support for the upper level as well as the back of what would eventually be retaining walls and tunnel portals. I used my speed square to figure out what angles I should cut the various pieces to I could join them together with relatively tight seams. I worked my way around the layout cutting pieces to size as I built the retaining wall slash supports. Sadly, the camera focus remained off for most of this, but you see what the final arrangement of pieces looked like in the end. I simply glued all of these pieces to the layout base and to each other using wood glue. Here are the approximate lengths and angles for each of these segments. If you are building this yourself you don’t need to follow these measurements exactly.
Everyone needs a speed square by the way: https://amzn.to/3IxfJ6h


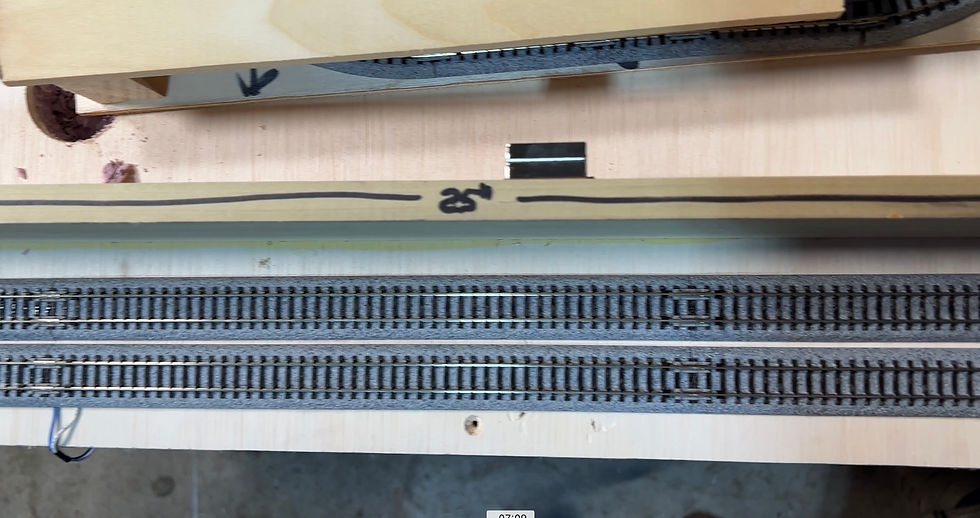


I also added some additional wood supports in the interior, making an enclosed box in the middle of the layout. I’ll probably add some additional supports closer to the edges as well to make sure the middle level is supported well.
Once the glue on those supports had dried, I placed the 3/4” plywood base for the middle level on top of the lower level. I used a pencil to trace along the edge of the supports so I would know where to make my cuts.
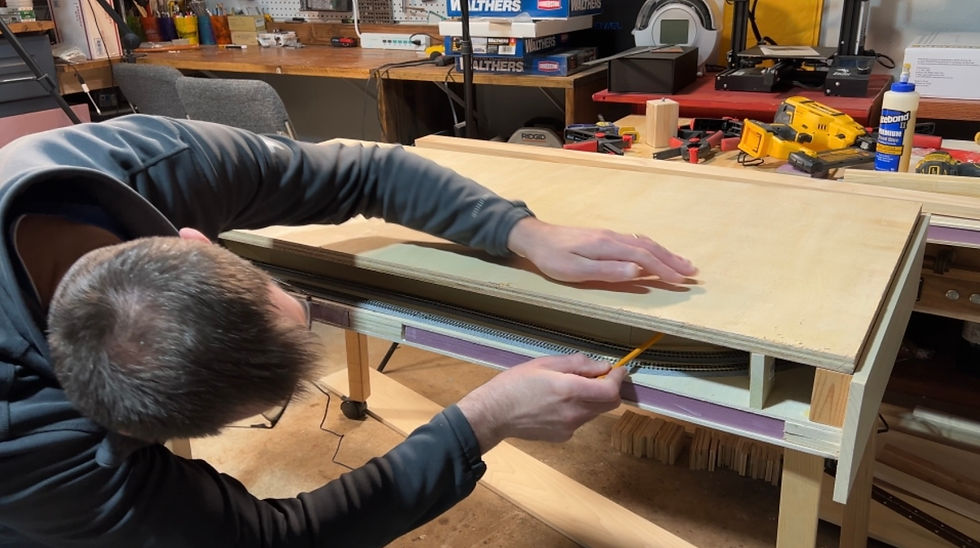
Then I flipped the board over and used another wood board as a straight edge to help fill in the gaps in the marks I made. I used my circular saw to make all the cuts, but had to finish a few corners off with a hand saw.


A good sanding was needed, and after blowing the sawdust off with my leaf blower, I test fit the middle level base on the lower level. Luckily, things lined up great and no further cutting was needed.

With the plywood cut to size, I took another four foot long piece of half inch by six inch poplar, and ran a bead of glue along one edge. I then secured the board to the plywood with several brad nails.
I needed to trim one side slightly, so I did that with my circular saw, and then sanded the cut edge smooth.

I salvaged a brass hinge from an old bookcase that had a drop down desk and decided to use that hinge on this project. I roughly measured things to get the hinge approximately centered, and then used some tape to hold it in place. I put in several screws and then tested the hinge and played around with trying to figure out a solution for a magnetic latch.

I had different cabinet latches, but I needed something that would strongly pull the lid down since there was a very slight bow in the plywood. What ended up working was taking two of the cabinet latch pieces that had steel plates and magnets, and attach them to the bottom together. Then, I used two neodymium magnets on the lid portion. These have metal pieces that are screwed into the lid, and then the magnets just snap into the holders and are held in place by magnetism alone. The two neodymium magnets and the magnets and steel plates on the bottom make for a very strong attachment. You actually have to pull pretty hard on the lid to get it to open.


With that latch figured out, I went back and added in all the remaining screws to the hinge.
I also salvaged a pair of support arms from the same desk I took the hinge from, and attached those to the base and lid. You can see what the support arms look like here once they were attached. Fortunately, there is enough clearance under the support arms when they are in the down position to allow for trains to pass underneath them. They work well, and the tension knobs can be turned tighter or looser to control how easy or hard it is to open and close the lid.

These won’t work to keep the lid from closing, a pneumatic arm would be needed for that, but they keep the lid from opening more than 90 degrees. I used a pneumatic arm on my 1x5 foot N scale switching layout as the image below shows.
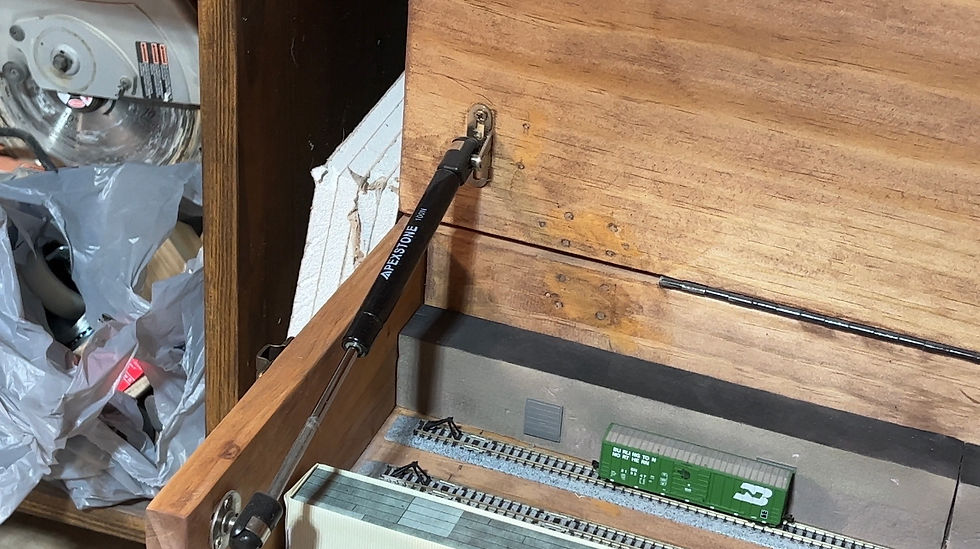
Since the other side of the lid will have a lot of weight on it from the third level and all the structures and scenery, keeping the lid from falling all the way open is the main concern. It is possible I’ll need to replace the screws in the lid with small bolts instead, but it seems to work well for now. I might instead add a couple of wood blocks to the back of the lower level to prevent the top section from opening past 90 degrees.
With the hinge and support arms attached, I worked on attaching the sides to the middle level. I measured and cut both sides to length, then cut the corner off one side, leaving about 1.5” below the diagonal cut. This was just to prevent there from being a sharp corner that I would likely repeatedly scrape up my arms on while working on the layout. I could have just rounded the corner off, but liked the look of the diagonal cut.

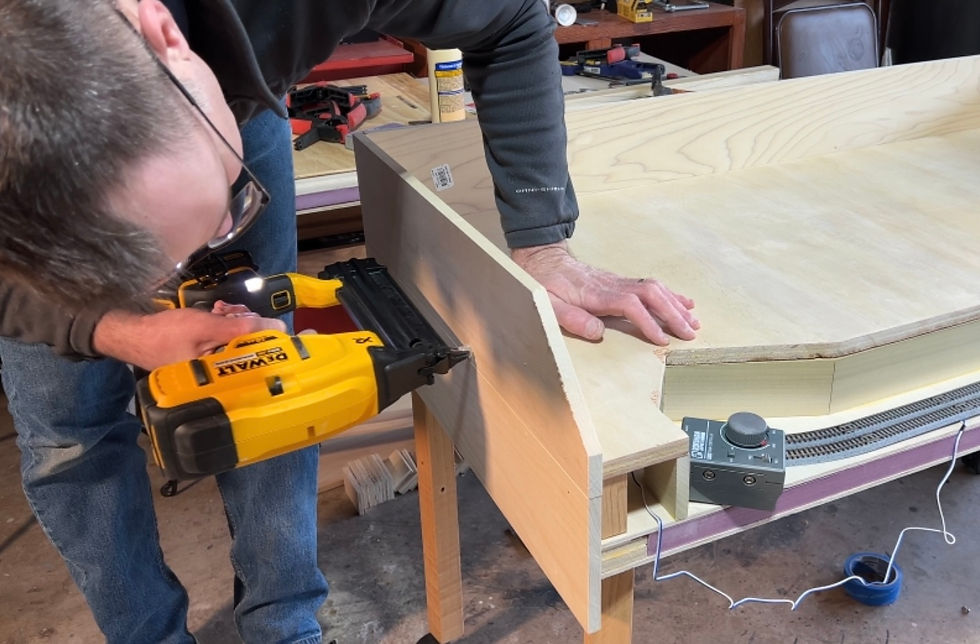
To attach the side pieces I applied glue along the edges of the side, and then used some brad nails along the edges. A couple nails ended up poking out the sides of the back board, but it was easy to break those off with a pair of pliers. I got the other side attached and then worked on cutting out the board for the top level. I placed the track loop on another piece of quarter inch birch plywood, and then used a ruler to mark out where I wanted to cut the plywood. I cut out the piece of plywood with my circular saw, sanded the edges, and then test fit it on the layout.
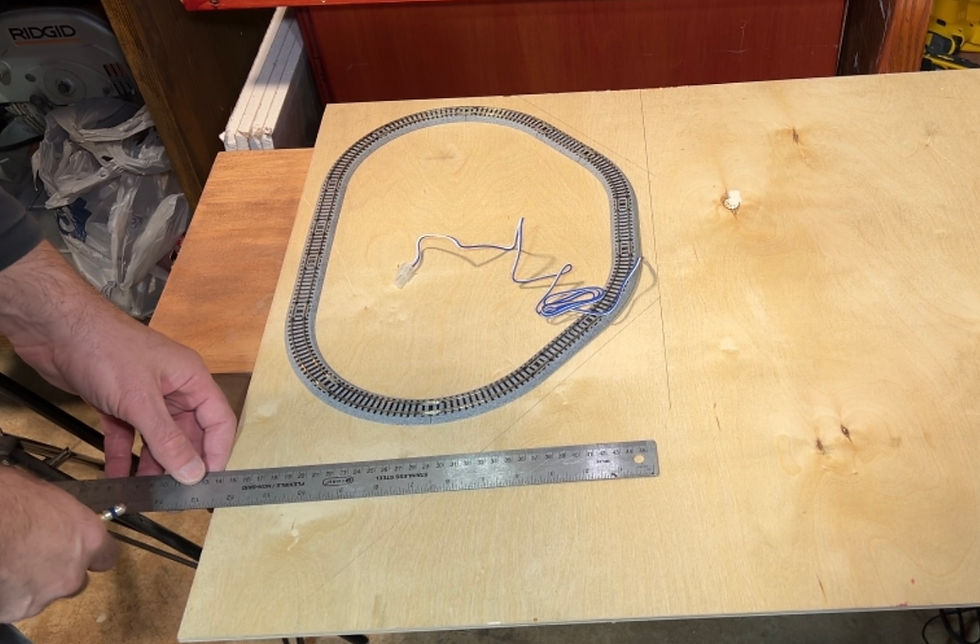
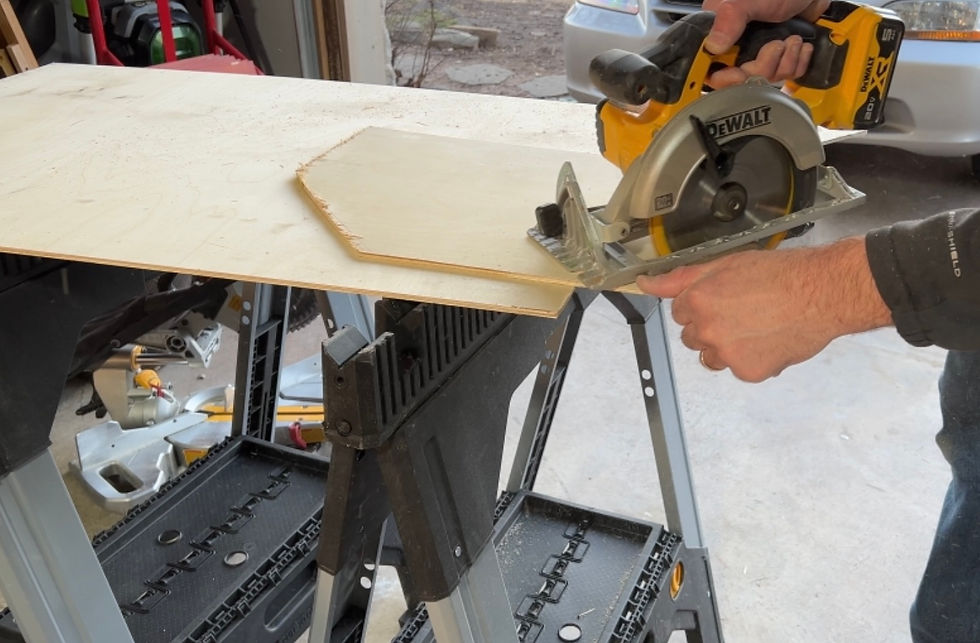
Since a corner was going to overhang the lower level, I had to cut an inch or so off of one side. Instead of using the saw, I just repeatedly scored the wood with a knife until I was able to break off the section I wanted to remove.
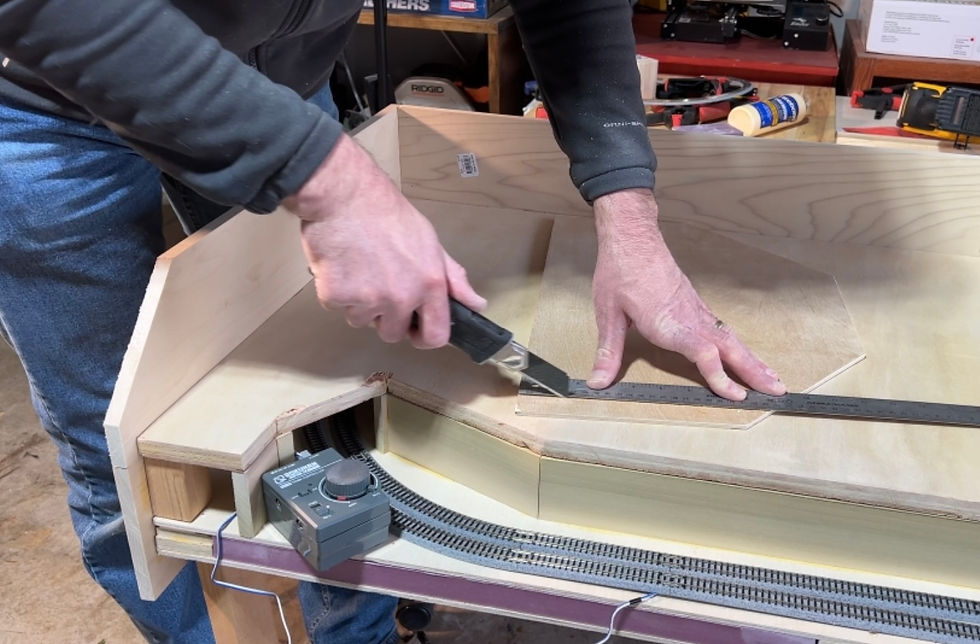
In order to make sure the supports for the top level wouldn’t interfere with the track on the middle level, I needed to assemble the track for the middle level. I followed the track plan I had pulled up on my iPad, and worked on assembling the pieces. This was a bit tricky in a few spots, since not all the Kato track pieces are labeled the same and I had already tossed all the packages that said what track piece was what. So, in some cases, I had to actually measure the pieces to be sure I was using the right one. But, I was able to get everything assembled without too much trouble and everything fit nicely.

For the upper level supports, I used a piece of 1x3 clear pine. I first cut pieces to go up against the back and sides of the layout, and then along the front edge. Like with the lower level supports, I worked my way around, figuring out what angles to cut each piece in order to match up with the upper level and to fit tightly with each other. I marked out where I needed the support pieces with a pencil, and then glued down each piece, making sure they aligned with my markings when I put them back down. I cut and glued some additional support pieces in the interior as well so the thin upper level base would have plenty of support.
If you are building this layout yourself, you don’t need to follow these measurements exactly, but here are measurements to various points in inches if you want to cut things about the same size.

Finally, I used 1x2 clear pine to create a fourth level that would hide part of the third level track loop and allow me to raise up some of the structures in that area for more visual interest on the layout. I’ll also eventually extend the side walls in this area to protect the top level buildings. Anyway, you can see that this layout should have a lot of visual interest with all the various levels. I may have some structures span multiple levels as well for even more visual interest.

Anyway, that wraps up the construction of the benchwork for the 2x4 foot N scale project layout. In the next update I’ll get the Kato Unitrack all installed and the basic wiring completed so I can run trains on all of the track loops.
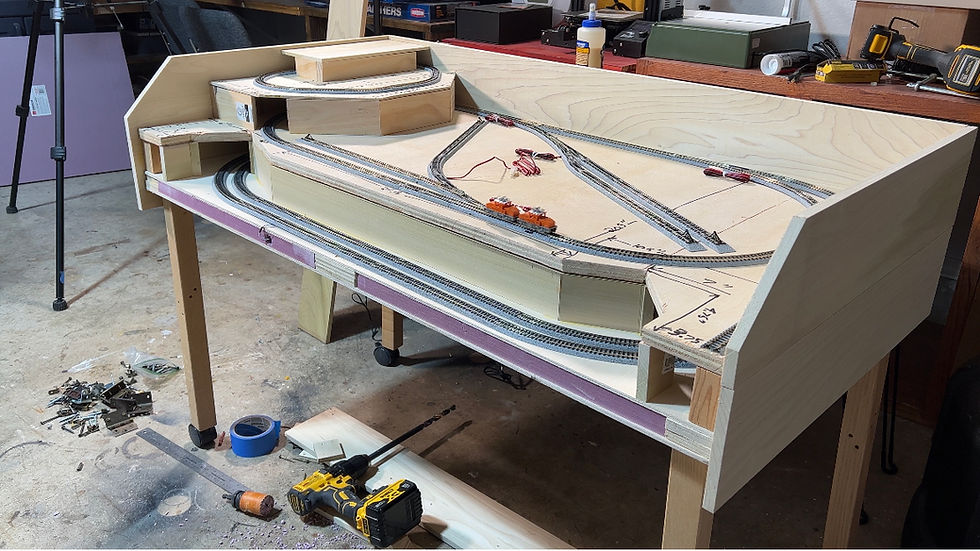

You can watch the video version on YouTube below.
Comments